Key Points
- Fertiliser production underpins our ability to feed the global population but accounts for ~2% of GHGs due to the highly emissive and energy-intensive Haber Bosch process, used to produce Ammonia.
- The emerging technologies to decarbonise fertiliser production include: Optimised application, Blue and Green Ammonia and Bio-inspired approaches.
- However, low carbon alternatives struggle to compete on price due to the use of cheap natural gas in the Haber Bosch process.
- The key metric driving adoption by customers is $ per unit N delivered by the fertiliser.
The Highly Emissive Incumbent
The Haber Bosch (HB) process for Ammonia (NH3) synthesis has been one of the greatest enablers for population growth in human history, facilitating an eight-fold increase in agricultural food yield since 1950.
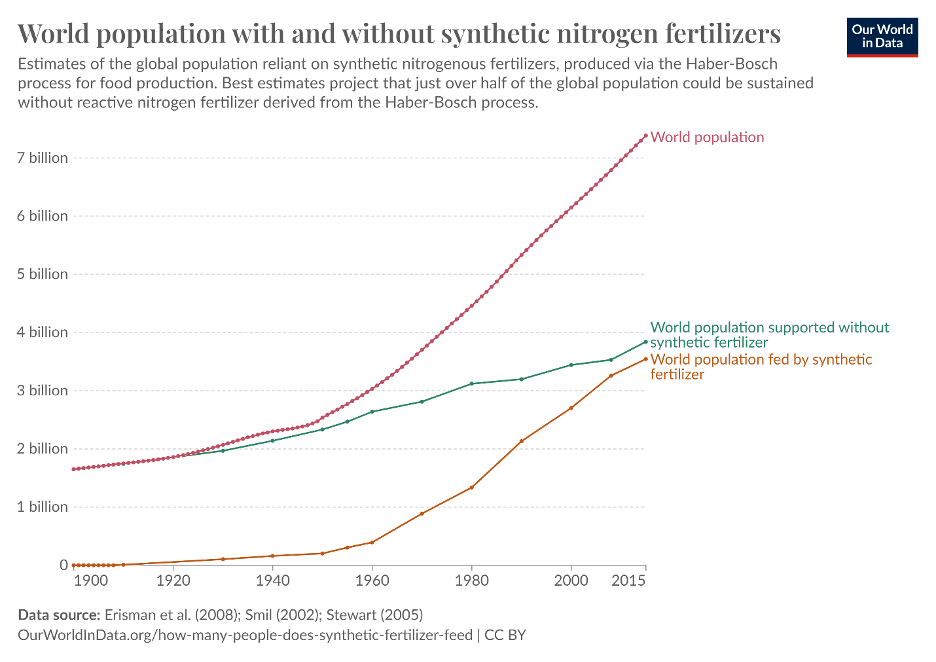
Nitrogen (N), one of the key molecules in ammonia (NH3), is naturally found in soils and is crucial to plant growth. However, these natural levels are not sufficient for crop growth at the scale of human agricultural production, and N is well documented to be the limiting factor in plant growth. Synthetic fertilisers enable greater agricultural yields and, as Figure 1 shows, sustains about half of the global population. Ammonia and its derivatives make up two thirds of all global fertilisers, largely due to its low cost per kg of N.
The HB process was invented in 1913 as a method of transforming inert (but abundant) atmospheric N2 into a nitrate to make explosives for the German war effort. It wasn’t until afterwards that it was realised that this form of N was also highly accessible by plants.
Nitrogen itself makes up 78% of the Earth’s atmosphere. Naturally, it exists as two nitrogen atoms triple bonded together, one of the strongest known atomic arrangements. The key innovation of the HB process was the realisation that the triple bond could be broken under immense pressure and temperatures (~450C and 200-300 atm) in the presence of an iron catalyst. The inventors realised that by splitting the hydrogen out from natural gas, and introducing this hydrogen into the reaction chamber, the N bonded to the hydrogen and the resulting molecule was stable at room temperatures and pressures.
The rest is history and now many of the world’s most ubiquitous fertilisers including Urea, Ammonium Nitrate and Ammonium Sulphate are derived from HB produced NH3. It’s worth highlighting that there are many applications for ammonia, for example as both a hydrogen carrier and carbon free fuel for shipping. But, we will stick to fertiliser in this post.
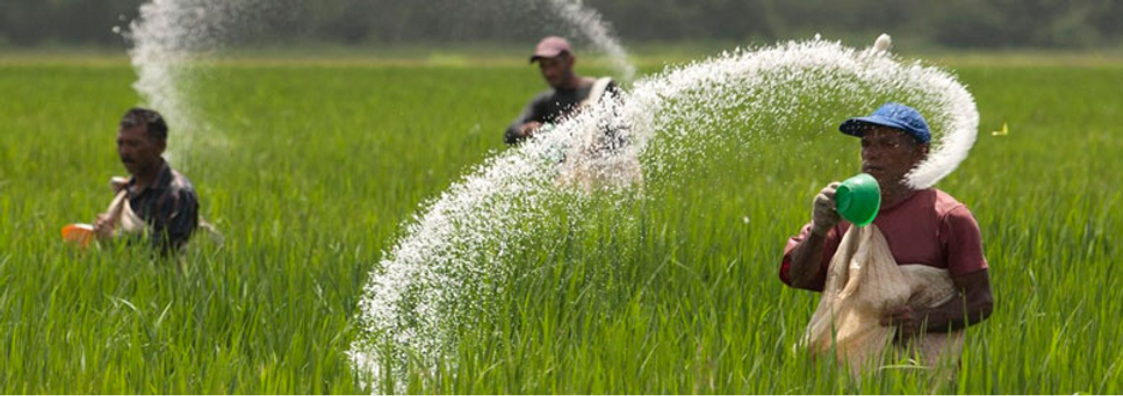
Emission Base
The high pressure and temperature in the HB reaction mean that ammonia production is incredibly energy and carbon emission intensive. In fact, globally, 1-2% of energy consumption, 3-5% of natural gas consumption, and ~2% of GHG emissions come from fertiliser production.
On a mass basis, ammonia generation is twice as emission intensive as crude steel fabrication and four times that of cement production. 2.4 tonnes of carbon dioxide is emitted during the HB process for every tonne of ammonia generated.
These emissions stem from two sources. The first is the steam methane reforming step to reduce natural gas to hydrogen. This accounts for 73% of the process emissions and is the driver for green hydrogen approaches. The second, smaller emissions source is the exhaust from the combustion of fossil fuels to produce the high temperature and pressure operating conditions required in the reaction chamber.
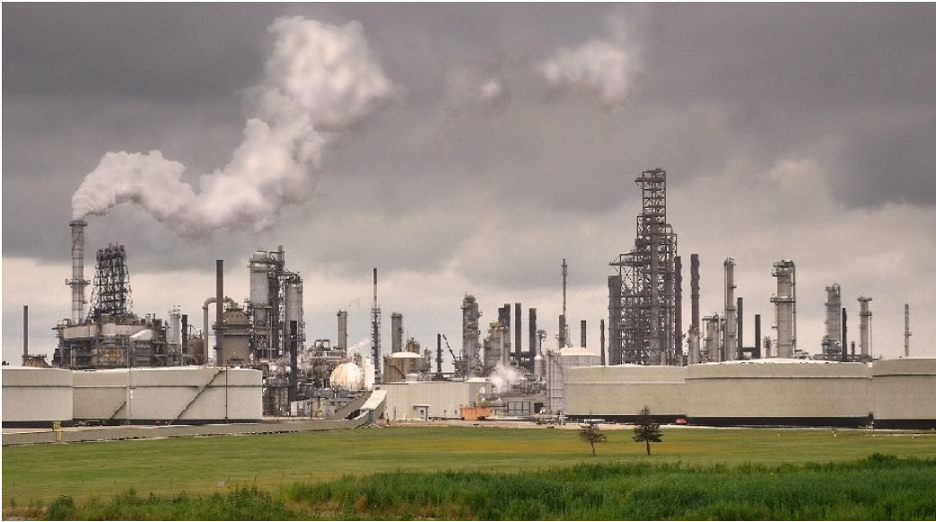
Often overlooked are the downstream emissions of ammonia. Once applied, plants typically only absorb 50% of the fertiliser, and the rest is left to run into waterways and escape into the atmosphere. This results in the emission of large quantities of nitrogen oxides which, on a mass basis, have a 300x warming effect compared with CO2. Strategies and technologies to mitigate this do exist, with coated urea pellets (protected urea) used to direct urea to the plant, reducing emissions by up to 79% compared with normal urea. These technologies do tend to command a slight cost premium, however.
Decarbonising Fertilisers
How can fertiliser production be decarbonised?
Optimised application strategies are interesting. A significant body of literature suggests that farmers often over fertilise due to poor feedback loops on soil nitrogen levels and a fear of under fertilised crops. These approaches look to reduce fertiliser consumption to the optimal level, minimising wasted fertiliser and hence cost. However, they do not eliminate production emissions. These strategies complement low/zero carbon fertilisers to reduce but are not a full solution.
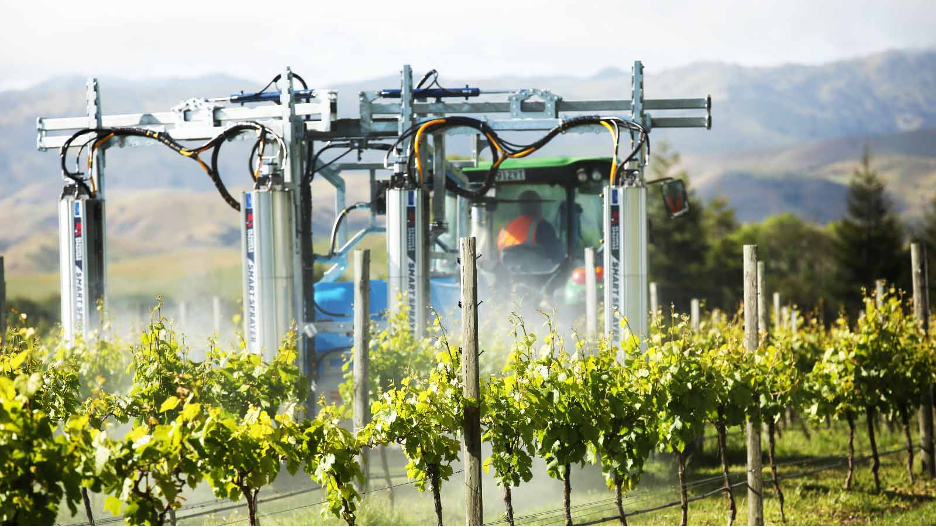
Blue ammonia is promising because adding carbon capture to existing processes could, in theory, decarbonise the ammonia industry overnight. However, the cost of carbon capture is still extremely high and struggles to match cheap natural gas; it is hard to imagine blue ammonia ever reaching cost parity to grey without market mechanisms such as government subsidies or carbon pricing.
This leaves green ammonia. Green ammonia includes everything from the electrification of the HB process to the synthesis of nitrogenous fertilisers via plasma. There are indeed many different pathways in the green ammonia space. In fact, we think green ‘ammonia’ is somewhat of a red herring. Green ‘fertiliser’ is a better label, as some approaches do not need to pass through the ammonia step. We take the view that the farmer will ultimately choose the cheapest, most effective, and most practical fertiliser, irrespective of its chemical composition – as long as N is chemically accessible to crops.
From our work, we believe technologies requiring a supply of green hydrogen typically do not meet the required $/kg N pricing, succumbing to the same headwinds faced by the broader green hydrogen industry. On the other hand, biological approaches supercharging natural nitrogen enhancement by adding nitrogen fixing microbes into the soil are nascent and suffer from environmental ecosystem forces that prevent their proliferation. The most commercially viable solutions that we’ve seen to date have offered low-cost N through efficient chemical pathways, leveraging proximate farm supply chains.
The Fertiliser Landscape
There are other factors beyond emissions that are causing changes in the nitrogenous fertiliser landscape. The price of Urea is heavily correlated with natural gas and geopolitical events, including the Russia Ukraine conflict, have resulted in a gas spot prices 640% higher in 2022 year-over-year. The continuing conflict has meant that prices have remained high, resulting in a global restructuring of energy trade networks.
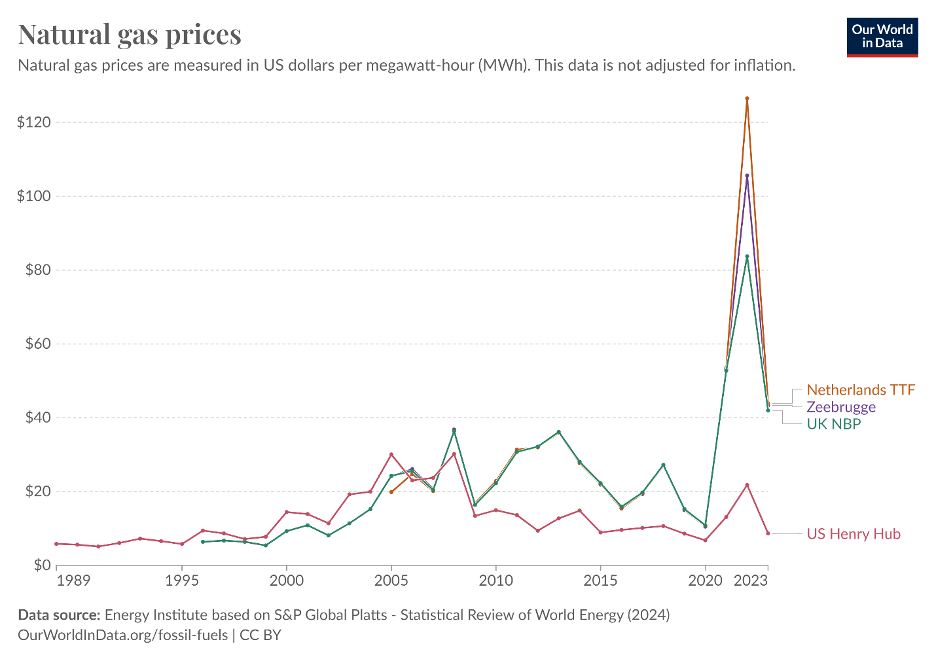
Europe has felt this more than most, where it has now been mandated that all EU countries will be independent of Russian gas by 2030. Positive steps have been made already, with Russian imports decreasing from 39% in Q4 2021 to 12% in Q1 2024. However, a much less debated topic is the growing reliance on Russian fertilisers. For the third month in a row, Russian fertiliser imports into the EU have increased, now reaching $188.8 million. This is the highest figure since the start of the conflict. Given the current political landscape, it’s likely that EU countries will also look to other sources.
Herein lies an opportunity for green fertiliser businesses. Existing nitrogenous fertiliser production is heavily centralised. Economies of scale and tight margins mean that large industrial sites make up the lion's share of the fertiliser market. These sites are incredibly CAPEX intensive and are sensitive to feedstock pricing. Many of the proposed ‘green’ solutions pursue decentralised production, in part because financing startups to build at this scale is challenging, but also as newer modular technologies are developed. While this model does require market adaptation there are many favourable characteristics including assured supply chain durability, decreased transportation costs and greater self-sustainability. It is our view that it is in this space that green fertiliser technologies stand to make an outsized impact.
Conclusion
Fertilisers are a critical component of our global food system but are far from climate friendly. The incumbent Haber-Bosch process to manufacture ammonia, the precursor to most nitrogenous fertilisers is dirty. Alternatives do exist and there is reason to be excited about innovations in various “green ammonia” technologies. Moreover, the current climate for both natural gas and fertilisers more broadly has driven prices up, creating the perfect storm for new technologies to disrupt fertiliser emissions and cost.
Twynam was founded as an agricultural business and still has strong roots in the Australian farming industry. This has meant that we have been able to take a customer centric approach towards analysis of low-carbon N fertiliser solutions. Adoption is driven by price and practicality; the key metric being $/kg N delivered to the soil. It is our firm belief that for any low-carbon technology to disrupt the market, it must outperform incumbent approaches without subsidies or carbon credits.